BOLT CARRIERS
BOLT CARRIERS
Accu-Cut has the right gear solution for you.

ACCU-CUT BORE SIZING MACHINES
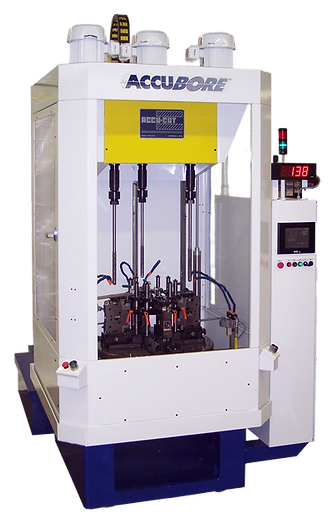


ACCU-CUT DIAMOND BORE SIZING SYSTEMS, INC.
Accu-Cut’s machine division was born out of customer demand for statistically capable machines that use Accu-Cut’s high performing diamond tools. Accu-Cut sold its first machine in 1988 and has since sold over 500 machines across North America, South America, Europe, Middle East and Asia.
Accu-Cut machines are made-to-order, specifically engineered for your unique application. They are modular “automotive duty” machines, built to run 365 days/year and last 20+ years.
Accu-Cut machines are fully customizable to meet your needs. We will recommend the best possible machine configuration to meet your application requirements while keeping to your budget.
-
Part length range: 0.5mm (0.02”) to 500mm (20.0”)
-
Bore size range: 1.0mm (0.040”) to 200.0mm (8.0”)
-
Parts per cycle: 1 to 10+
-
Spindles (tool stations): 1 to 16+
-
Spindle head motors: 1 to 6+
-
Load/unload: manual, pick-n-place, or robot with conveyor, bowl feeder, and magazine/tray options
-
Feed: ball screw driven with encoder or servo feedback
-
Gaging: pre-process, poke-yoke, in-process, and post-process gaging options with data capture/export and analysis with auto audit cycles
-
Fixtures: rigid, semi-rigid X-Y floating, or gimbaled
-
Operator safety: interlocked barrier guarding with e-stops and optional light curtain
-
Machine safety: auto torque sensing, overload protection and poka-yoke crash prevention
-
Controls: Allen-Bradley or Siemens
-
Filtration system: filter bag, cyclonic filter, magnetic separator, or paper-magnetic options with pump and tank
-
Lubrication: automatic lube option with PLC control and monitoring
-
Tool adjustment: automatic tool compensation option and quick tool change option
Accu-Cut machines are flexible and can be built to handle multiple families of parts with the appropriate change parts. Our machine and fixture solutions are designed to accommodate your production needs while minimizing changeover time. In addition, Accu-Cut machines can be retooled to handle new applications as older applications reach the end of their lifecycle. Accu-Cut has also retooled over 25 competitor machines (both honing and bore sizing) to utilize our superior technology to bring these machines up to Accu-Cut standards, saving customers time and money to launch production.
Accu-Cut tools and machines have a 35 year history of providing statistically capable results at a low per piece cost. If you want to learn more about how Accu-Cut can provide you with a cost effective, turn-key bore sizing solution, please feel free to contact our customer service team at Service@AccucutDiamond.com.
DID YOU KNOW...
-
that Accu-Cut machines played a critical role in Ford’s initiative to install airbags in all of their automobiles back in 1989?
-
that Accu-Cut diamond bore sizing machines have replaced million dollar traditional honing and grinding machines at a fraction of the cost?
-
that there are 25+ year old Accu-Cut machines that are still in service today?
-
that Accu-Cut connecting rod machines are the industry standard with over 20 machines worldwide that produce a total of 30M+ parts per year?

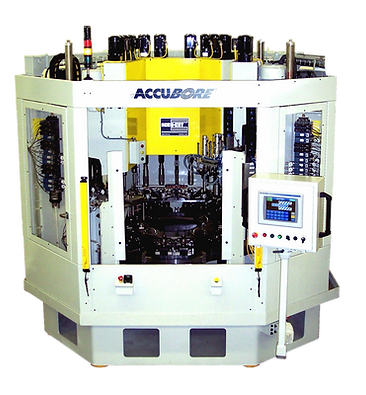
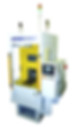




ALL ACCU-CUT MACHINES RECEIVE LIFELONG TECHNICAL SUPPORT
ACCU-CUT CUSTOMIZES MACHINES TO YOUR APPLICATION
HERE ARE A FEW EXAMPLES:


1-SPINDLE MACHINE
MODEL 1SM-S
4-SPINDLE MACHINE

MODEL 4SM-I



MODEL 6X3SMC-IAG


6-SPINDLE MACHINE
MODEL 6SM-I

MODEL 2X3SMC-IG




MODEL 2SM-I

MODEL 3x2SMREC-IG

WITH SHUTTLE FIXTURE
WITH INDEXING
18-SPINDLE MACHINE
3-PARTS PER CYCLE WITH
AUTOMATION, GAGING, AUTO TOOL COMPENSATION, AND DATA COLLECTION
6-SPINDLE MACHINE
TWO 3-SPINDLE HEADS, TOOL COMPENSATION, PRE-GAGE, SAFETY LIGHT CURTAIN, AND RETRACTABLE BARRIER GUARD
WITH INDEXING AND 3 SPINDLE HEAD MOTORS
MODEL 2x3SMC-IG
6-SPINDLE MACHINE
WITH INDEXING, AUTO TOOL COMPENSATION AND GAGING
2-SPINDLE MACHINE
WITH INDEXING
6-SPINDLE , RECIP AND EXPAND MACHINE
WITH INDEXING, IN-PROCESS GAGING AND AUTOMATIC TOOL COMPENSATION




