BOLT CARRIERS
BOLT CARRIERS
Accu-Cut has the right gear solution for you.

APPLICATIONS

ACCU-CUT TOOLS AND MACHINES have proven successful over countless applications throughout our 35 year history. Manufacturers have trusted Accu-Cut to develop cost effective, SPC capable solutions to give them the competitive edge to win projects and meet their cost and quality objectives.
Interested in how Accu-Cut can provide you with a cost effective solution for your application? Please feel free to contact us at Service@AccucutDiamond.com.

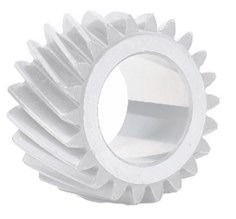
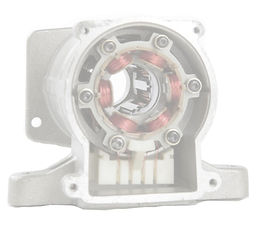


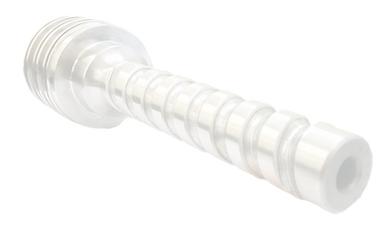


CONNECTING ROD
Accu-Cut introduced diamond bore sizing to powder metal connecting rods with 0.006” stock removal in 1990 and has since been the industry leader. With a 0.003” stock removal, our 6-pass process (3-pass pin, 3-pass crank) can achieve a roundness of 0.00005”, surface finish of 8 Ra, bore size CPK > 2, and cycle time of < 10 seconds. Our process also corrects bend and twist.
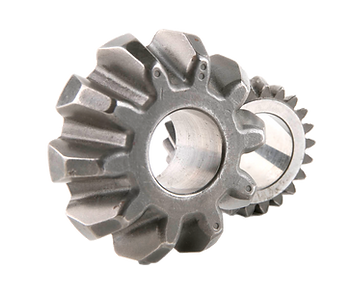
DIFFERENTIAL AND PINION GEARS
Accu-Cut’s bore sizing process on forged steel differential gears can remove as much as 0.007” stock in a 0.835” long bore with 5 tool passes to achieve a roundness of 0.00004”, surface finish of 8 Ra, bore size CPK > 2, and cycle time of < 20 seconds. Shorter lengths can achieve even shorter cycle times.
HYDRAULIC VALVE

Accu-Cut has revolutionized the bore sizing of cast iron hydraulic valves by achieving high statistical process control that eliminates valve ID classification. Our process and tools can achieve stock removal of 0.020”, bore size CPK > 2, surface finish of 5 Ra, roundness of 0.000050”, and a cycle time of 30 seconds across a 7” bore.
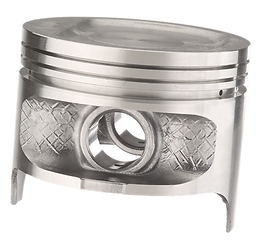
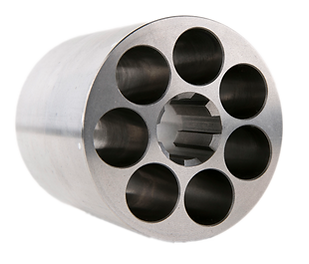
PISTON
Accu-Cut’s diamond tool technology processes interrupted bores such as those on pistons, achieving 0.003” stock removal, bore size CPK > 2, surface finish of 11 Ra, roundness of 0.000050”, at a cycle time of 20 seconds.
ROTARY PISTON PUMP - BLIND BORE
Accu-Cut’s blind bore process can handle applications with little relief, achieving stock removal of 0.002”, roundness and straightness of 0.000025”, bore size to within 0.000030”. and a surface finish of 6 Ra.
HARD BROACHING
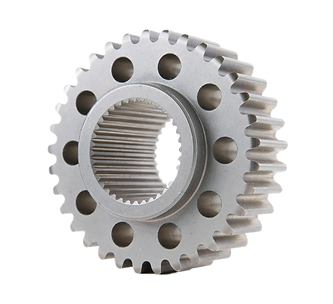
Accu-Cut’s diamond hard broaching process is one-of-a-kind and is most widely used to correct internal spline distortion post heat treat. Our process is able to correct involute form as well as major and minor diameter, all with a single tool. Gear manufacturers rely on this technology to eliminate interference cause by heat treat distortion. In addition, our process can handle irregular bores such as D-shaped, double D-shaped, lobed shaped, and other non-circular bores.
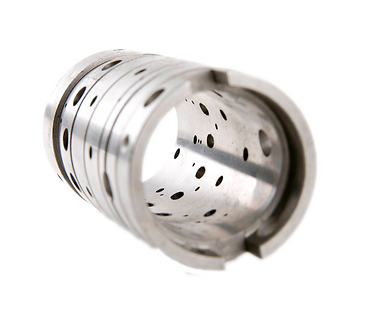
STEERING SLEEVE
Accu-Cut’s micro-cutting technology performs exceptionally well on thin-walled parts. Unlike conventional honing, which pressurizes and distorts the part, our micro-cutting tools provide minimal pressure for higher precision, statistically capable bore sizing. This steering sleeve was bore sized to a roundness and straightness of 0.000020” and a cylindricity of of 0.000020”.
ENGINE VALVE HEAD
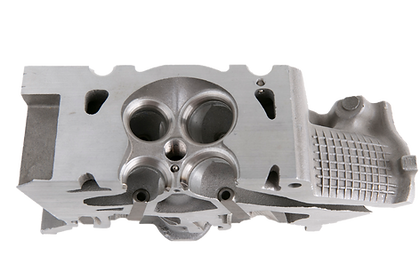
Accu-Cut’s valve seat tools are ideal for eliminating leakage in engine valve heads, removing between 0.0005” to 0.0025” in less than 30 seconds. This simple diamond tool has helped automotive manufacturers salvage countless engine heads that originally failed due to leakage, saving hundreds of thousands of dollars.



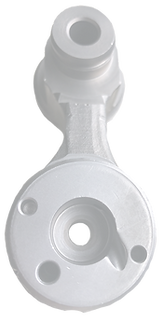
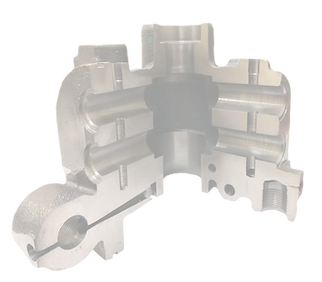
